Autonomous Package Induction for a Global Parcel Carrier
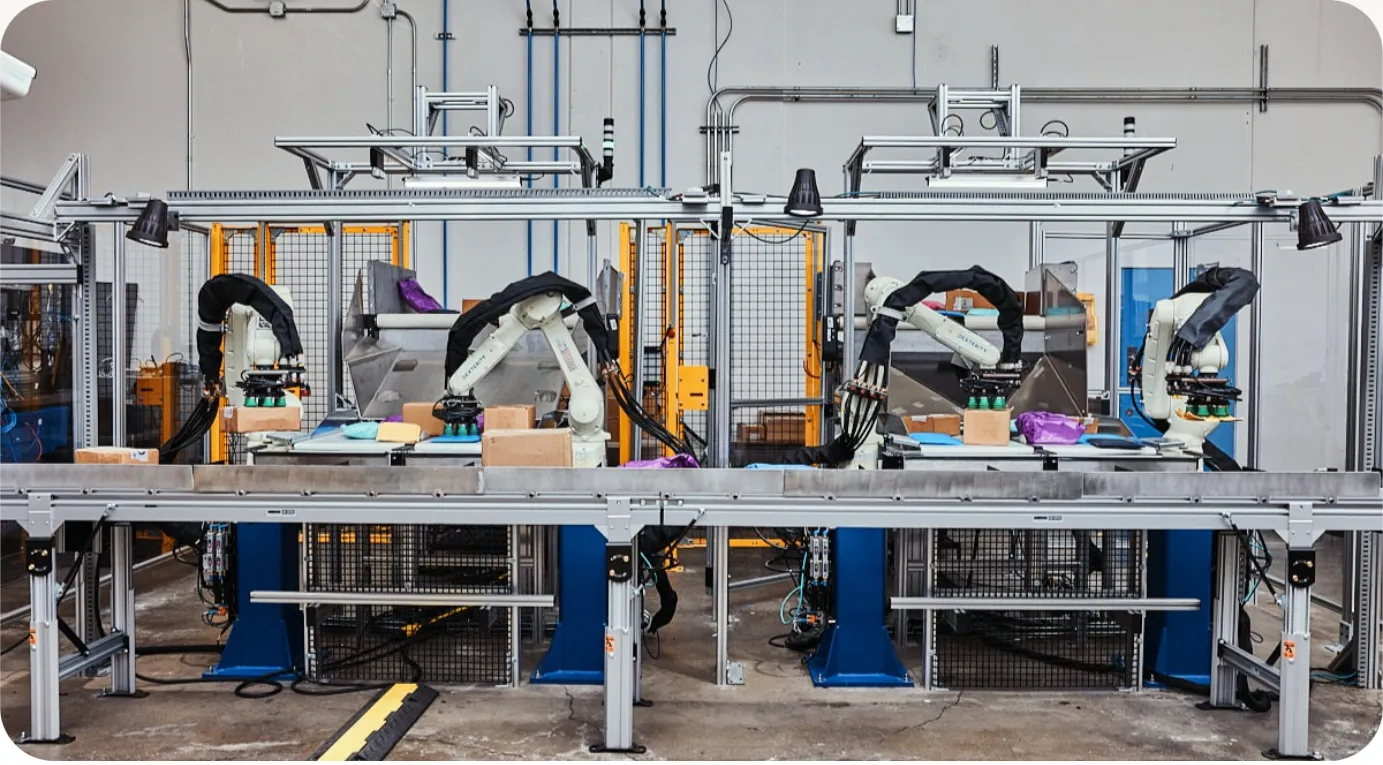
Dexterity's Full Task Robots Transform Parcel-Induction Processes by Automating Workflows With Minimal Infrastructure Modifications
Dexterity's robotic systems are in production 24/7 powering parcel sortation, package fulfillment, case level picking, and palletizing for large enterprise customers. Unlike generally available robots, which require installing expensive and bulky material handling equipment,Dexterity's robots operate within existing workflows at beyond human rates and with ahuman-sized footprint. Our robots share networked intelligence to coordinate actions ,improve performance, and provide real-time insights into upstream and downstream operations.
Sort & Induct Anything
"I've seen all the robotics companies, and you're a significant step above everyone on the totem pole."
Research & Development Manager
Transforming the operations of two of the largest parcel carriers.
Dexterity leverages computer vision and learning to segment parcels, plan their picks, identify labels, and improve system performance over time.
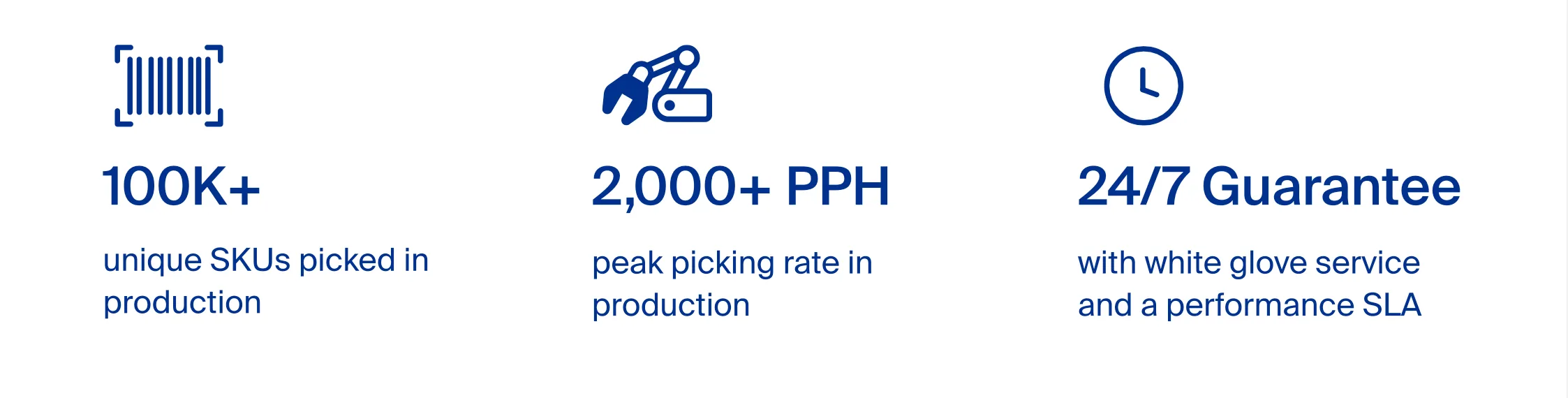
Problem
One of the largest parcel carriers in the world faced an uphill battle to keep pace with increasing package volume while facing an intense labor shortage. These challenges, ongoing over the past five years, were amplified by the COVID-19 pandemic leading to unsustainably low labor availability, high turnover, and intense recruiting competition.
In response, the carrier decided to introduce robots: they engaged with dozens of robotic automation providers, yet all failed to handle live production.
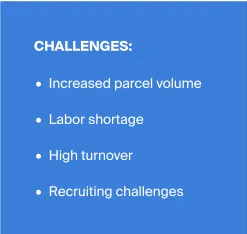
Key Requirements
1) Super human speed in parcel picking (~2,000 PPH)
2) Low capex integrated with existing warehouse infrastructure.
3) Flexibility to handle piles of flats, boxes, bubble packs, polybags, non-inductables
4) Human fallback and ability to remove robot from picking station in <5 mins
Dexterity's Mandate
To deliver transformative impact, the customer worked together with Dexterity to introduce robotics into its parcel singulation and induction process. This use case, to pick items out of a bulk pile and place on to a tilt-tray sortation system, had broad applicability across the customer’s operations. Robots were required to operate at a very high speed (2,000+ picks per hour peak) while accurately picking a near- infinite variety of packages, boxes, and polybags from cluttered flowing chutes packed with items. More importantly, the robots had to minimize human interventions, manage irregulars, and unjam chutes as needed.
Dexterity's Approach
Dexterity’s platform provides intelligent controls, scheduling, and machine learning-based computer vision to whatever robotic arms and grippers are needed to perform intelligent tasks. These baseline software tools enable rapid authoring of new robot behaviors to address a wide range of material handling tasks, including singulation and induction.
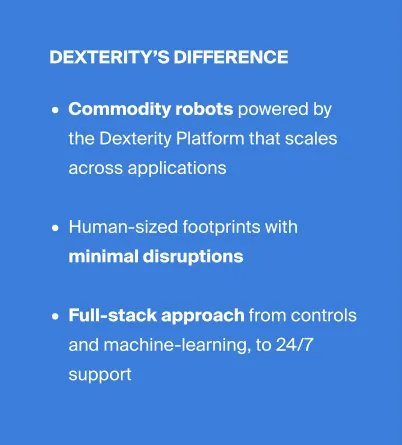
Before any design work started, Dexterity worked closely with the customer to determine how to deploy the system with minimal workflow disruption. This meant the robots would have to pick to existing high-speed conveyor systems. The customer also wanted the robots to fit within existing 1m square picking stations so they could easily interchange human and robotic labor at their singulation stations. All these features enabled the customer to deploy robots with minimal additional infrastructure cost or downtime during the installation process.
Dexterity selected the hardware that would meet the customer’s performance and pricing requirements. By using Kawasaki arms, the carrier had a hardware solution that could easily scale across their global operations. Additional design included the modularity of a dual arm station to hit the customer’s desired peak induct speed and a six-sided barcode scanner that matched human scan rates before slotting.
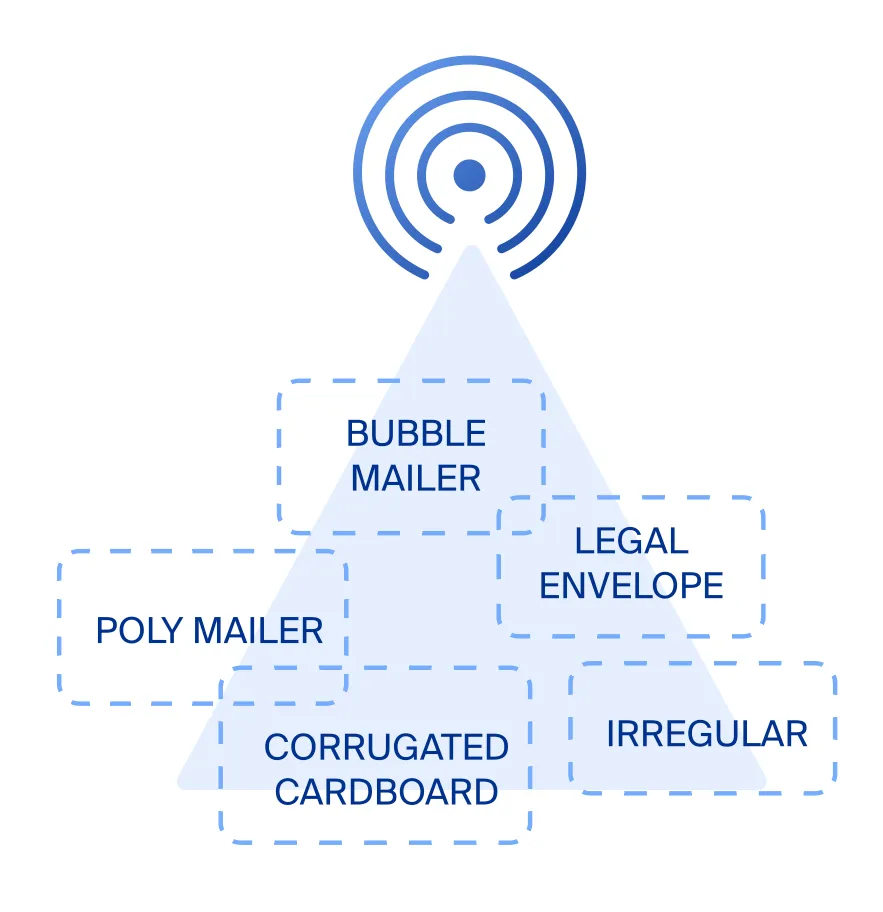
To ensure that the automation systems delivered on the quality and speed expectations of the customer, Dexterity delivered a slot monitoring system that identifies and tracks system metrics. Integrating this system into the carrier’s operations system enabled the customer to minimize double picks to a single tray and to determine the occupancy and utilization rate of each one of their sorters. The slot monitor system, combined with robot pick data, provides granular insights into overall facility performance that the customer never knew they could access - and function equally well on manual induction lines.
Complicated production environments is where Dexterity's robot intelligence really shines.Each scene presented to the robot is new, and the data generated from picking in these environments is used to reinforce good robot behavior. Production experience increases the intelligence and performance across the entire robot fleet.
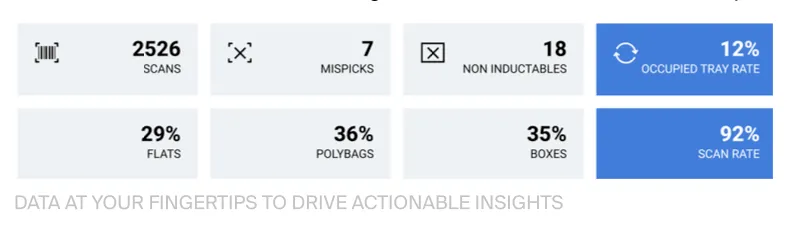
Results
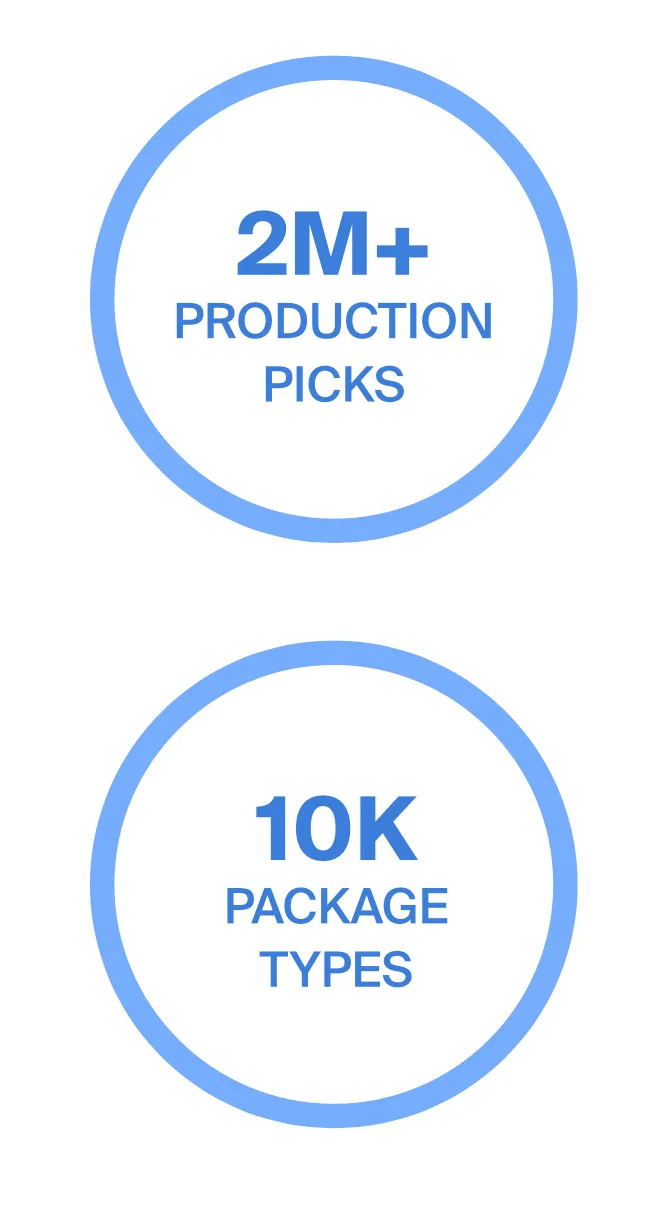
Dexterity’s commercial model enabled the customer to demonstrate immediate ROI. The customer bought robots, licensed Dexterity’s software, and had minimal additional infrastructure costs, meaning they could demonstrate savings on the first day of deployment.
Since April 2021, Dexterity’s robots have been running full shifts picking at rates that exceed the customer’s 2,000 pph benchmark, and have made over 2 million production picks to date. The facilities withDexterity robots also feature the carrier’s highest mix of packages including flats, bubble packs, poly bags, and irregulars.
Since deployment, Dexterity’s robots have handled over 10,000 different package types in production. As with all Dexterity customers, the carrier received a 24/7 guaranteed support SLA that meant they could rely on their new robots through two service peaks.